ニッケルの加工について詳しく解説!|非鉄金属加工
- 短納期対応
- 大型機械加工
- 非鉄金属
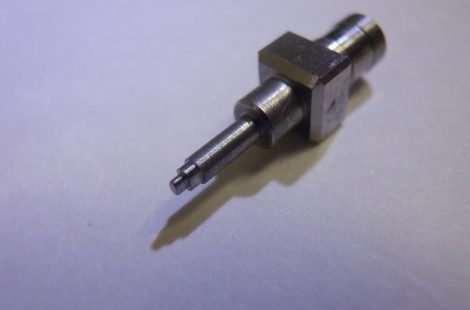
非鉄金属 ニッケル
非鉄金属は様々な種類に分けることができます。そこで今回はその1つであるニッケルに関した内容をご紹介させていただきます。
>>「非鉄金属」に関するお問合せ・見積依頼はこちら
ニッケルは、銀白色の光沢を持つ金属で、鉄やコバルトと同じく鉄族元素に分類されます。様々な特性を持つことから、多くの産業分野で欠かせない材料となっています。 ここでは、ニッケルの基礎知識から用途、そして将来展望まで詳しく解説していきます。
ニッケルの基礎知識
ニッケルは、以下のような優れた物理的特性を持っています。
- 耐熱性: 高温下でも強度や耐食性を維持し、融点は1455℃と高く、ガスタービンやジェットエンジンなどの高温環境下で使用される部品に最適です。
- 耐食性: 酸化や腐食に強く、特にアルカリに強い耐性を示します。そのため、化学プラントや海洋環境で使用される機器にも利用されています。
- 磁性: 強磁性体であるため、磁石に引き寄せられます。この特性を利用して、モーターや発電機、磁気記録媒体などに利用されています。
- 展延性・延性: 薄く延ばしたり、線状に引き伸ばしたりすることが容易なため、加工性に優れています。箔や線材などに加工され、様々な用途に利用されています。
また、化学的特性としては、以下のような点が挙げられます。
- 耐酸性: 多くの酸に対して耐性を示しますが、硝酸のような酸化性の酸には溶解します。
- 耐アルカリ性: アルカリに対しては非常に強い耐性を持ち、腐食されにくいという特徴があります。
ニッケル合金の種類と特徴(純ニッケル、ニッケル基合金、その他合金)
ニッケルは、純ニッケルとして使用されるだけでなく、様々な元素と合金化することで、さらに優れた特性を持つ材料となります。主なニッケル合金には、以下のような種類があります。
- 純ニッケル: 高純度のニッケルで、耐食性や耐熱性が求められる化学プラントや電子部品などに使用されます。
- ニッケル基合金: ニッケルを主成分とし、クロム、モリブデン、鉄などの元素を添加した合金です。高温強度、耐食性、耐酸化性に優れており、航空機エンジン、ガスタービン、化学プラントの配管などに利用されます。代表的なニッケル基合金には、インコネル、ハステロイ、モネルなどがあります。
- その他合金: ステンレス鋼、銅ニッケル合金など、ニッケルを含む様々な合金が存在します。ステンレス鋼は、ニッケルを添加することで耐食性が向上し、キッチン用品や建築材料などに広く使用されています。銅ニッケル合金は、海水に強い耐食性を持ち、造船や海洋開発に利用されています。
ニッケルの用途
ニッケルは、その優れた特性から、様々な分野で利用されています。
- 航空宇宙: ジェットエンジン、ガスタービンなど、高温・高圧環境下で使用される部品にニッケル基合金が利用されています。
- 自動車: 排気ガス浄化装置の触媒担体、バッテリー、燃料電池などにニッケル合金が使用されています。
- 化学プラント: 反応容器、配管、ポンプなど、耐食性・耐熱性が求められる部品にニッケルやニッケル合金が利用されています。
- 電子機器: 電極、リード線、コネクタなどにニッケルやニッケル合金が使用されています。
- エネルギー: 火力発電、原子力発電などの発電プラント、風力発電、太陽光発電などの再生可能エネルギー分野でもニッケル合金が使用されています。
ニッケルの様々な加工方法とその特徴
ニッケルは、その優れた特性を生かして、様々な加工方法が用いられます。ここでは、ニッケル加工の代表的な方法である切削加工、塑性加工、溶接加工、そして特殊加工について、それぞれの特徴や用途を詳しく解説していきます。
切削加工 – 旋削、フライス、研削
切削加工は、切削工具を用いてニッケル素材を削り、目的の形状に加工する方法です。ニッケル加工において最も一般的な加工方法であり、様々な形状の部品を製作することができます。
旋削加工:工作機械を用いた精密な加工
旋盤と呼ばれる工作機械を用いて、回転するワーク(加工物)を切削工具で削る加工方法です。主に、円筒形や円錐形、ネジ山などの形状に加工する場合に用いられます。旋削加工は、高い寸法精度と表面粗さを実現できることが特徴です。
ニッケルは加工硬化しやすいという性質がありますが、切削条件を適切に設定することで、高精度な加工が可能です。また、ニッケルは熱伝導率が低いため、切削時に発生する熱を効率的に逃がす冷却方法を採用することが重要です。
>>大型旋盤加工および旋盤加工とは?当社の保有設備や加工実績について詳しくご紹介
フライス加工:多様な形状に対応する加工技術
フライス盤と呼ばれる工作機械を用いて、回転する切削工具でワークを削る加工方法です。平面、溝、曲面など、多様な形状に加工することができます。フライス加工では、工具の種類や切削条件を変えることで、様々な加工に対応できます。
ニッケル加工においては、加工硬化による工具摩耗や、熱伝導率の低さによる工具の損傷に注意が必要です。耐摩耗性に優れた工具材料を使用したり、切削油剤を効果的に使用したりすることで、これらの問題を解決することができます。
研削加工:表面仕上げに欠かせない技術
砥石を用いてワークを研磨し、表面を滑らかにしたり、寸法精度を高めたりする加工方法です。切削加工の後に行われることが多く、最終的な仕上げ工程として重要な役割を担います。
ニッケルは、研削加工によって美しい鏡面仕上げを得ることができます。ただし、ニッケルは研削熱の影響を受けやすいため、適切な研削条件や冷却方法を選択することが重要です。
塑性加工 – 鍛造、圧延、プレス
塑性加工は、ニッケル素材に力を加えて変形させ、目的の形状に加工する方法です。塑性加工によって、強度や靭性を向上させることができます。
鍛造加工:強度と靭性を向上させる伝統的な技術
高温に加熱したニッケル素材を金型で挟み込み、ハンマーやプレス機で叩いて成形する加工方法です。鍛造加工によって、結晶組織が緻密化し、強度や靭性、耐疲労性が向上します。
ニッケル合金は、高温強度が高いという特性を持つため、鍛造加工に適しています。航空機エンジンやガスタービンの部品など、高い強度が求められる部品に利用されています。
圧延加工:板状の製品を製造する技術
ニッケル素材をローラーで圧延し、板状に成形する加工方法です。圧延加工によって、板厚や幅を調整することができます。
圧延加工は、大量生産に適した加工方法であり、ニッケル合金の板材は、航空機、自動車、建築など、様々な分野で利用されています。
プレス加工:複雑な形状を成形する技術
ニッケル素材を金型でプレスし、複雑な形状に成形する加工方法です。プレス加工は、大量生産に適しており、様々な形状の部品を効率的に製造することができます。
ニッケル合金は、プレス加工性にも優れており、自動車部品、電子部品、日用品など、幅広い用途に利用されています。
溶接加工 – TIG溶接、MIG溶接、レーザー溶接
溶接加工は、熱や圧力を用いてニッケル素材を接合する方法です。ニッケル合金は、溶接性にも優れており、様々な溶接方法が適用できます。
TIG溶接:高品質な溶接に最適な方法
タングステン電極を用いたアーク溶接です。溶接部の品質が高く、精密な溶接に適しています。ニッケル合金の溶接に広く用いられており、航空機や原子力プラントなど、高い信頼性が求められる分野で利用されています。
MIG溶接:効率的な溶接を実現する方法
溶加材を用いたアーク溶接です。TIG溶接に比べて溶接速度が速く、効率的な溶接が可能です。ニッケル合金の溶接にも適用でき、自動車部品や建築構造物など、幅広い分野で利用されています。
レーザー溶接:精密な溶接に適した方法
レーザー光を用いた溶接です。熱影響範囲が狭く、歪みが少ないため、精密な溶接に適しています。ニッケル合金の溶接にも適用可能で、電子部品や医療機器など、微細な部品の溶接に利用されています。
その他の溶接方法:抵抗溶接、電子ビーム溶接
ニッケル合金の溶接には、TIG溶接、MIG溶接、レーザー溶接以外にも、抵抗溶接や電子ビーム溶接などの方法が用いられます。抵抗溶接は、電流を流して発熱させることで金属を接合する方法で、自動車の車体製造などに利用されています。電子ビーム溶接は、電子ビームを照射して金属を溶融させる方法で、高真空下で高品質な溶接を行うことができます。
特殊加工 – 放電加工、レーザー加工
特殊加工は、切削加工や塑性加工では難しい形状や材質の加工に用いられる方法です。ニッケル合金の加工にも、特殊加工技術が活用されています。
放電加工:複雑な形状や硬い材料に対応
電極とワークの間で放電を起こし、金属を溶融・除去することで加工する方法です。複雑な形状や硬い材料の加工に適しており、金型製作や精密部品加工に利用されています。ニッケル合金のような難削材にも適用可能です。
レーザー加工:高精度・高効率な加工を実現
レーザー光を用いて、金属を切断、穴あけ、溶接などを行う加工方法です。高精度・高効率な加工が可能で、ニッケル合金の加工にも利用されています。近年では、レーザー加工技術の進歩により、微細加工や複雑形状の加工も可能になってきています。
ニッケル加工の課題と解決策
ニッケル加工は、その優れた特性を得る一方で、加工の難しさという側面も持ち合わせています。加工硬化や熱伝導率の低さ、工具摩耗など、特有の課題を克服することが、高品質なニッケル製品を製造する鍵となります。ここでは、ニッケル加工における課題と、その解決策をプロの視点から詳しく解説していきます。
加工硬化
加工硬化が起こるメカニズム
ニッケルは、加工によって硬化し、切削加工が困難になる性質があります。これは、加工によって材料内部の結晶構造が変化し、硬度が増加するためです。加工硬化が起こると、工具摩耗が激しくなり、加工精度が悪化したり、表面にひび割れが発生したりする可能性があります。
ニッケルの加工硬化は、特に冷間加工で顕著に現れます。冷間加工とは、材料を再結晶温度以下で加工する方法です。冷間加工では、材料内部に歪みが蓄積しやすいため、加工硬化が起こりやすくなります。
対策:適切な工具選択、切削条件の調整、冷却方法
加工硬化を抑制するためには、以下の対策が有効です。
- 適切な工具選択: 超硬合金やサーメット、CBN(立方晶窒化ホウ素)、ダイヤモンドなどの耐摩耗性に優れた工具材料を使用します。また、工具の形状やコーティングも、加工硬化の抑制に影響を与えます。
- 切削条件の調整: 切削速度や送り量、切込み深さを適切に調整することで、加工硬化を抑制することができます。一般的に、切削速度を上げると加工硬化は抑制されますが、工具摩耗が激しくなる可能性があります。送り量や切込み深さを小さくすると、加工硬化は促進されますが、工具寿命を延ばすことができます。
- 冷却方法: 切削時の発熱を抑えるために、クーラントを効果的に使用します。クーラントの種類や流量、噴射方法などを最適化することで、加工硬化を抑制することができます。
熱伝導率の低さ
熱伝導率の低さによる問題点
ニッケルは、熱伝導率が低いという性質があります。そのため、切削加工時に発生する熱が工具に集中し、工具寿命の低下や加工精度の悪化につながることがあります。また、熱によって材料が変形し、寸法精度が狂う可能性もあります。
熱伝導率の低さは、特に高速切削や深切削を行う際に問題となります。高速切削では、切削速度が速いため、単位時間あたりに発生する熱量が多くなります。深切削では、切込み深さが大きいため、工具と材料の接触面積が大きくなり、熱がこもりやすくなります。
対策:冷却の効率化、工具の形状最適化
熱伝導率の低さを克服するためには、以下の対策が有効です。
- 冷却の効率化: クーラントの種類、流量、噴射方法などを最適化することで、工具の冷却効果を高めます。また、切削油剤を使用することで、冷却効果と潤滑効果を同時に得ることができます。
- 工具の形状最適化: 熱がこもりにくい形状の工具を使用します。例えば、チップブレーカーを設けることで、切屑を細かく砕き、熱の発生を抑えることができます。
工具摩耗
ニッケル加工における工具摩耗の特徴
ニッケルは、硬度が高いため、工具摩耗が激しいという課題があります。工具摩耗は、工具寿命の低下や加工コストの増加につながるため、抑制することが重要です。
ニッケル加工では、特に、凝着摩耗、拡散摩耗、酸化摩耗などが発生しやすいです。凝着摩耗は、工具と材料が接触することで、材料の一部が工具に付着して摩耗する現象です。拡散摩耗は、高温下で工具と材料の原子が相互に拡散することで、工具が摩耗する現象です。酸化摩耗は、高温下で工具表面が酸化することで、摩耗する現象です。
対策:耐摩耗性工具、コーティング、切削条件の最適化
工具摩耗を抑制するためには、以下の対策が有効です。
- 耐摩耗性工具: 超硬合金、サーメット、CBN、ダイヤモンドなどの耐摩耗性に優れた工具材料を使用します。
- コーティング: 工具にコーティングを施すことで、耐摩耗性を向上させます。例えば、TiN(窒化チタン)コーティング、TiAlN(窒化チタンアルミニウム)コーティング、ダイヤモンドライクカーボン(DLC)コーティングなどが有効です。
- 切削条件の最適化: 切削速度や送り量を最適化することで、工具摩耗を抑制します。
表面欠陥
表面欠陥の種類と発生原因
ニッケル加工では、表面に様々な欠陥が発生する可能性があります。主な表面欠陥には、以下のようなものがあります。
- バリ: 切削加工の際に、材料が切削刃から剥がれることで発生する突起です。
- ひび割れ: 加工硬化や熱応力などによって発生する亀裂です。
- クレーター摩耗: 工具の摩耗によって、加工面に形成される凹みです。
- ビルトアップエッジ: 切削時に、材料が工具に付着して形成される突起です。
これらの表面欠陥は、製品の品質や性能に悪影響を与えるため、防止することが重要です。
対策:加工条件の管理、表面処理
表面欠陥を防止するためには、以下の対策が有効です。
- 加工条件の管理: 切削速度、送り量、切込み深さ、クーラントなどの加工条件を適切に管理することで、表面欠陥の発生を抑制することができます。
表面処理: 加工後に、表面処理を行うことで、表面欠陥を修正したり、表面の特性を向上させたりすることができます。例えば、研磨、バフ研磨、ショットピーニングなどが有効です。
ニッケルの加工事例・実績
専用治具の丸棒
こちらは、専用治具に使用される丸棒部品です。 外形φ50、長さ194mmの素材にφ22.45mmのガンドリル加工を深さ170mmで実施しました。
材質のSUS304は、オーステナイト系ステンレス鋼であり、主な合金としてクロム18%、ニッケル8%が添加されています。 磁性が無く、マグネットにつかない材質です。また耐食性、強度等が優れているため、難削材の部類に入ります。
BTAガンドリル.COMでは、SUS304のような加工の難しい材質も長年の経験により対応可能です。 ニッケルが添加されたステンレス鋼のガンドリル加工でお困りの際は、是非一度ご相談ください。
非鉄金属の加工に関するよくある質問
Q.片側貫通は可能ですか?
A.基本的には両側貫通にて加工しておりますが孔径と長さによっては、片側貫通可能でございます。 詳細はお問い合わせにてご確認ください。
Q.どこまでの長さが加工可能ですか?
A.自動見積では2000mmまでですが、それ以上もケースによっては加工可能です。 詳しくは、お問い合わせください。
Q.孔径、孔の曲がりの公差はいくつ程度ですか?
A.孔径:±0.2~0.3程度 孔の曲がり:1mにつき1mm程度 ですが、小径の場合は曲がりが大きくなる場合があるため、別途お問い合わせにてご確認ください。
Q.加工面の面粗度はいくつ程度ですか?
A.標準では、Ra=25にて対応しております。
非鉄金属・ニッケルの加工をご検討の際は、メタナビにご相談ください!
非鉄金属の加工などにお困りの方は、メタナビにご相談ください。